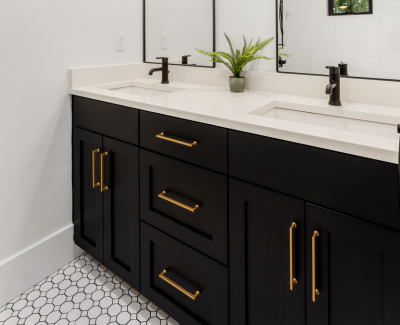
Hybond resolves 3D Pressing issue for bathroom manufacturer
Hybond recently provided technical support to a customer requesting assistance with their 3D pressing process. A bathroom manufacturer was experiencing issues with foils tearing in their presses, and whilst not an adhesive problem, as technical experts in all aspects 3D pressing, Hybond were able to provide free of charge assistance within the customer’s service package.
Read on to discover how intelligent auditing technology, plus decades of Hybond technical expertise led to a prompt diagnosis and resolution.
3D PRESSING – AN INTRO
Also known as vinyl or membrane pressing; this lamination technique is popular with those producing decorative furniture fronts within kitchen, bedroom and bathroom production. Raw MDF panels are spray-coated with adhesive, dried, and passed through a press where they are wrapped in decorative vinyl foil through exposure to temperature and pressure. The results provide many colourful and varied finishes.
THE ISSUE
Foils tearing in a customer’s 3D press system.
DIAGNOSIS
Hybond’s technical team completed a comprehensive 3D pressing audit at the customer’s site of manufacture. The team use data logging software connected via bluetooth to a dummy panel. The dummy panel is put through the pressing cycle as if it were an actual panel being processed, allowing our tech team to collect a series of data points in real time during the pressing process.
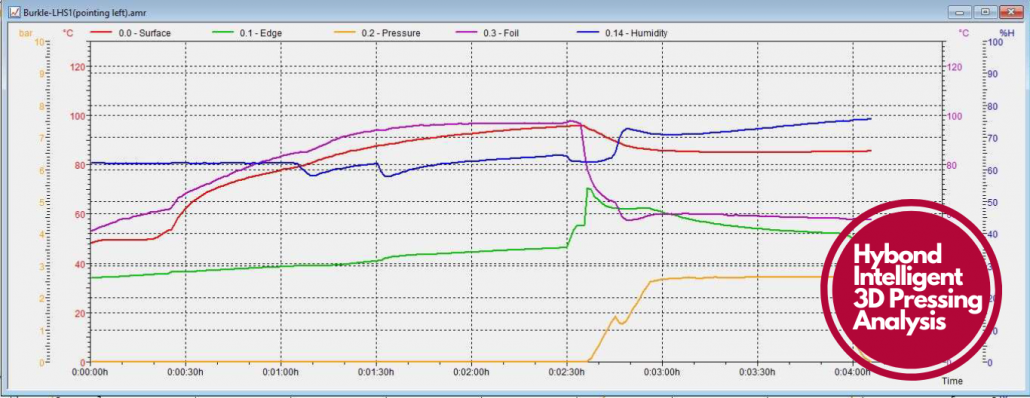
It can be observed that the foil temperature is being measured at over 100°C at certain points in the process. This is too hot.
THE RESULTS
The profile report produced was analysed fully by our team and discussed in detail with the customer. Some findings were as follows:
- A critical edge temperature was measured at 71°C, which is much higher than the 56°C needed to guarantee the correct adhesive crosslinking.
- The surface temperature at the bond line was showing as 95°C, and though this reading is normally hotter than at the sides, this is more heat than is necessary for this process.
RESOLUTION
Hybond concluded that the whole process was generating excess heat at the customer’s current press settings. Our team suggested there was plenty of scope to drop temps by 10°C or more, without compromising the edge temperature. The customer has been advised to bring the foil temperature max levels to around 90°C where they should see a significant improvement in press results.
Hybond Director Ross Dalrymple speaks further on Hybond’s 3D Pressing auditing service:
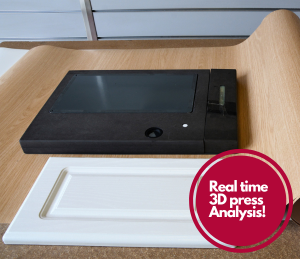
Ditch inaccurate & fiddly temperature testing strips!
“Operators of 3D pressing systems will be acutely aware how important it is to achieve precise temperature levels during the pressing process in order to avoid quality issues such as bubbling, tearing, and delamination. Many will be familiar with the use of disposable temperature strips for ascertaining heat levels within your system, these can be tiresome to use, often giving inaccurate readings and restricting the user to limited placement points. The beauty of our intelligent sensor panel is that it travels through the press system taking readings throughout, for example a vertical reading can be obtained measuring the temperature of the foil directly above the panel – the temperature at this position is critical as it will dictate how well the heat transfers to bond the foil securely to the exterior panel edge. When we consider end usage of such panels in kitchen or bathroom environments, it is essential there is no entry point for moisture, therefore the information obtained during our audit process has proven to be an essential tool in ensuring optimal quality output for our customers.”
WORK WITH US!
Do you have an adhesive challenge that our technical team can assist you with?
Would you benefit from a regular programme of audits?
Here’s just a few of the services the Hybond Laboratory can provide:
- Viscosity and solids analysis
- Peel, shear, and joint-break testing
- Microscope analysis of bond line integrity
- Accelerated aging testing
- Surface energy analysis
- Climate chamber testing
- Testing to industry standards such as those laid out by FIRA, IMO and more.
CONTACT Hybond today and a member of our technical team will assist you with your enquiry.